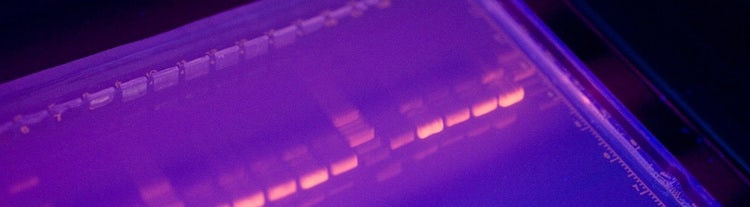
Aldevron Breakthrough Blog
Sterility Testing In the House
February 14, 2024 by Tom Kuhne
In-house capabilities for efficient production
Sterility testing is a critical feature in GMP manufacturing, ensuring that there are no viable bacteria, yeast or fungi in manufactured products. The USP<71> testing requirements are stringent, requiring additional time and resources to ensure those requirements are met and the finished products are sterile, and safe for use. Because of the tight specifications, it can be challenging to offer the service. But to meet client needs to speed timelines and improve efficiency, Aldevron has recently added sterility testing to its production capabilities.
An involved process
A big advantage for clients is the availability of in-house sterility testing which can reduce turnaround times and shipping risks. Our sterility testing for USP<71> capability officially launched this past August after a year of planning and implementation, which required many moving parts from multiple departments and outside vendors.
Due to the critical requirements of the process, we built suites specifically for our sterility isolator in Quality Control (QC). This involved building an anteroom qualified to allow for proper environmental controls, then adding an ISO 8 classified room in the QC area. This included bringing in utilities for the equipment, validating those utilities to meet clean dry air parameters, and performing Environmental Monitoring Performance Qualification (EMPQ) to determine the maximum occupancy of the room and identifying where EM sampling should occur.
When construction was nearing completion, the isolator was commissioned and brought on site, with Installation, Operational and Performance Qualification (IQ/OQ/PQ) performed by the validation department, QC, QA and consultants. To ensure equipment was working appropriately, microbiological qualification of load cycles was performed to determine what could be placed in the isolator, what parameters to use to achieve a 100% kill rate on biological indicators and in what configuration could the isolator be used. Once the decontamination cycles were validated, the pace of the QC collaboration with our facilities began to pick up.
Checking the system
Multiple validation and verification activities were performed within the isolator to show that the product being produced on site would not interfere with both types of USP<71> approaches; direct inoculation and membrane filtration. Tests were run on strategic buffers with different compositions and a variety of pH levels. This was done to:
- Test if filters would clog during membrane filtration
- Identify any potentials for inhibition of microbial growth from the final buffers
- Identify how much rinse volumes/maximum volumes to use for each of the two USP<71> methods.
QC also performed a false negative test intended to show that the container closure of the final product vials can withstand the harsh decontamination cycle without killing, inhibiting, or interfering with the test. This was done by inoculating organisms into multiple containers, exposing the containers to the decontamination cycle, and verifying that growth was not being inhibited by comparing the results to containers which had not undergone decontamination. At the same time, team members were developing documentation for internal processes and client services, all while considering isolator throughput and finding any factors that could reduce that throughput.
When all the pieces were in place, a decontamination hold time study was performed to show that the isolator could maintain a state of control for multiple days without decontamination being performed. This test allows Aldevron to run in the most efficient way.
What does this mean for you?
When it comes down to the basics, clients need compact timelines, lower production costs and a quality product. With the addition of our USP<71> capability, those requirements are now met in-house, without the need for the intermediate steps using third-party vendors. Turnaround times will be shortened, risk will be reduced from excessive shipping of materials, and will allow clients to have better visibility what stage of testing their product is in.